Emulsifiers
Emulsifiers in Oil-Based Mud: A Comprehensive Explanation:
Emulsifiers are surfactants (surface-active agents) composed of molecules with a hydrophilic (water-attracting) head and a hydrophobic (oil-attracting) tail. They stabilize mixtures of immiscible liquids, such as oil and water, by reducing interfacial tension and preventing separation.
Emulsion is a major part in an oil-based drilling fluid. An emulsion is a mixture of two immiscible liquid phases where one phase is dispersed into another. Basically, an emulsion is consisting of a continuous phase which is known as external phase, where the droplets are dispersed, and a dispersed phase which is defined as internal or discontinuous phase.
Types of Emulsions
Typically, if the oil is dispersed phase, the emulsion is named O/W, but if the aqueous medium is the dispersed phase, the emulsion is named W/O.
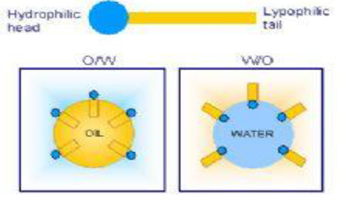
In the following animation, the light gray circular shape represents a water droplet. The small yellow spring-like structures are emulsifiers, with their heads attached to the water and their tails connected to the oil droplets.
Emulsions are found in different industries such as food, pharmaceutical, agricultural, cosmetics, and petroleum. Inherently, an emulsion is an unstable system due to the unfavorable contact between oil and water phases. Although, some emulsions are stable as a result of the small drop sizes and the existence of interfacial film, which surrounds the drops
To form an emulsion a mechanical force is required to disperse one phase into another. However, the emulsions formed without adding any surface-active material would not be stable, and the emulsion phases will start to separate in different layers based on their density differences. Therefore, we need to have intermediate agent (Emulsifier) that have partial solubility in each phase (oil and water), and finally a source of energy such as mixer to form the emulsion.
Oil-to-Water Ratios in Invert Mud
Invert muds are formulated with different oil-to-water ratios (OWR) depending on well conditions, formation properties, and drilling requirements. Common ratios include:
- 95:5 – High oil content, used when very low water phase activity is needed (e.g., deepwater drilling, shale-sensitive formations).
- 80:20 – Standard ratio for most OBM applications, offering a good balance of rheology, stability, and filtration control.
- 70:30 – Higher water content, improving cost efficiency while maintaining performance, but requiring stronger emulsification to prevent phase separation.
Emulsifier’s Role in Oil-Based Mud (OBM):
Oil-based muds are critical in drilling for their superior lubrication, high-temperature stability, and inhibition of reactive shale formations. However, they often incorporate brine (salty water) to adjust density, enhance cooling, or inhibit shale swelling. Emulsifiers are essential to maintain a stable invert emulsion (brine-in-oil), where brine is dispersed as tiny droplets within the continuous oil phase.
How Do Emulsifiers Work in Oil-Based Mud?
Emulsifiers work by surrounding water/brine droplets with a thin protective layer of surfactant molecules that prevent them from coalescing (merging together). This is done through:
- Molecular Structure – Emulsifiers are typically amphiphilic, meaning they have:
- A hydrophilic (water-attracting) head that associates with water.
- A hydrophobic (oil-attracting) tail that dissolves in the oil phase.
- Mechanism of Emulsification:
- When water (or brine) is introduced into the oil-based mud, the emulsifier surrounds each water droplet.
- The hydrophilic head stays in contact with water, while the hydrophobic tail stays in contact with the oil phase.
- This creates a barrier that prevents the water droplets from merging and settling out.
Importance in OBM:
- Stability: Prevents separation of brine and oil, ensuring consistent mud properties (e.g., viscosity, density).
- Performance: Maintains lubrication, reduces friction, and aids in carrying drill cuttings to the surface.
- Shale Inhibition: Brine (often with CaCl₂) prevents clay swelling; emulsifiers ensure its effective dispersion.
- Fluid Loss Control: Stabilized emulsion minimizes leakage into formations, preventing damage and circulation loss.
- Temperature Resistance: High-performance emulsifiers withstand downhole heat without degrading.
Following are emulsifiers that are used in invert mud:
- Primary Emulsifier
- The primary emulsifier is responsible for the initial formation of the water-in-oil emulsion in invert mud.
- It reduces the interfacial tension between water and oil, allowing water droplets to disperse within the continuous oil phase.
- Secondary Emulsifier
- The secondary emulsifier enhances the stability of the emulsion formed by the primary emulsifier.
- It helps control fluid loss, maintain proper rheology, and further reinforce the emulsion structure.
- Wetting Agent
- The wetting agent ensures that drilled cuttings and solids are preferentially wetted by oil rather than water.
- It prevents solids from agglomerating and helps keep them dispersed within the mud system, reducing issues like accretion and sticking.
Electrical Stability (ES) Test
- Purpose: Measures the strength of the emulsion by quantifying the voltage required to break it.
- How it works:
- A probe is inserted into the mud, and voltage is applied until the emulsion breaks (current flows).
- Higher ES values indicate a more stable emulsion (typical range: 300–1,000+ volts).
- Interpretation:
- Low ES = Poor emulsion stability (e.g., <300 V).
- Sudden drop in ES during drilling may indicate contamination (e.g., water influx, solids) or emulsifier degradation.